The No.1 Essential Machine for Good Waste Compaction Densities – Landfill Compactors
Landfill compactors play a crucial role in landfill waste management, as they are responsible for efficiently compacting and reducing the volume of solid waste in landfills.
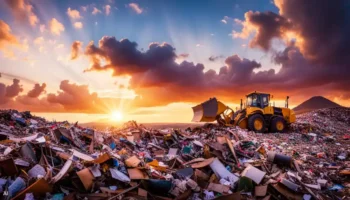
A landfill compactor is, in essence, a bulldozer with steel wheels that are fitted with spikes, lugs or bars for compression and traction purposes.
The configuration of the wheel spikes lugs, or bars is very important for good compression of the waste and reliable traction, for the best performance.
These heavy-duty machines, often weighing over 100,000 pounds, are not only powerful but also come with a significant price tag. In this article, we will explore the essential features of landfill compactors and delve into the costs associated with owning and operating these machines.
Essential Features of Landfill Compactors:
Robust Construction:
Landfill compactors are built to withstand the harsh environment of landfills. They feature a heavy-duty frame and reinforced components to ensure durability and longevity.
High Compaction Force:
These machines are equipped with powerful compaction mechanisms that exert immense force on the waste material. This force helps to compress the waste, reducing its volume and creating more space in the landfill.
Spiked Wheels:
Landfill compactors often have spiked wheels to provide better traction and stability on uneven and soft surfaces. These spikes penetrate the waste, allowing the compactor to manoeuvre effectively and exert maximum compaction force.
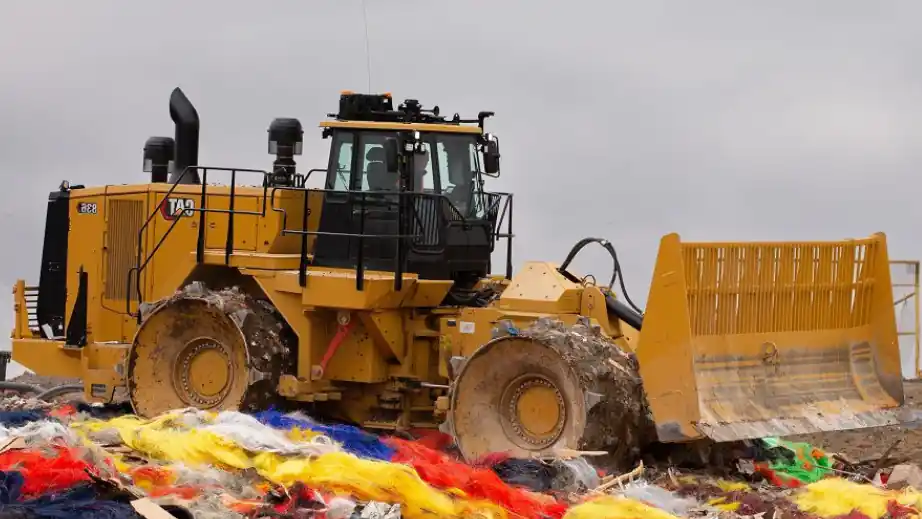
Sealed Cab:
Landfill compactors come with a sealed and pressurized cab to protect the operator from the hazardous gases and odours present in landfills. The sealed cab also reduces noise levels, ensuring a safer and more comfortable working environment.
Waste Management Systems:
Many modern landfill compactors are equipped with advanced waste management systems. These systems include onboard scales, GPS tracking, and telematics capabilities, allowing operators to monitor and optimize compaction operations.
Costs Associated with Landfill Compactors:
Initial Purchase Cost:
The cost of a landfill compactor can vary depending on its size, brand, and features. These machines can range from hundreds of thousands to millions of dollars. Generally, larger compactors with more advanced features tend to be more expensive.
Maintenance and Repairs:
Proper maintenance is crucial for the efficient and reliable operation of landfill compactors. Regular servicing, component replacements, and repairs contribute to the overall cost of owning these machines. It is essential to factor in the cost of maintenance when budgeting for landfill compactor operations.
Fuel and Operating Costs:
Landfill compactors consume a significant amount of fuel due to their size and power requirements. The cost of fuel, lubricants, and other consumables should be considered when calculating the operating costs of these machines.
Training and Operator Costs:
Operating a landfill compactor requires skilled and trained operators. Investing in training programs and hiring experienced personnel adds to the overall cost of owning and operating these machines.
Enhancing Landfill Compactors: Overcoming Challenges and Optimizing Performance
Introduction
Early landfill compactors faced several challenges, which have since been addressed through technological advancements. In this comprehensive exploration of landfill compactors, we will delve into the reported issues with early models, discuss the essential features of modern compactors, and consider various factors that influence the choice of landfill mobile plant.
Reported Issues with Early Landfill Compactors
In the early days of landfill compactors, two primary issues were frequently reported.
First, these compactors had a tendency for their wheels to pick up refuse, especially in wet weather conditions. Second, instability was a concern due to their high centre of gravity.
The configuration of the track and wheel spikes played a crucial role in addressing these issues.
However, it was discovered that tipping waste in shallower layers often helped overcome these difficulties.
Modern Landfill Compactors
Modern landfill compactors have come a long way in terms of design and performance. They are equipped with steel wheels featuring spikes, lugs, or bars for both compression and traction. The careful configuration of these track and wheel spikes is essential.
While they operate in a very hostile environment perched on waste, and exposed to the waste, they may not match the performance of civil engineering earthworks equipment, but they offer reliable waste density when operated correctly.
They hugely raise efficiency in landfill operations when compared with the previous use of tracked vehicles (bulldozers) until they were invented back in the 1970s.
Additional Equipment and Considerations
In landfill operations, you might encounter other equipment such as scrapers, towed or independently powered, which are used for various tasks like stripping, storing, and replacing topsoil and subsoil.
Mechanical diggers and trenching equipment are also common for on-site work.
Furthermore, when considering the purchase of landfill compactors or bulldozers for refuse handling, several key features must be taken into account.
These include operator protection with cabs equipped with roll bars, specialized blades for refuse handling, four-wheeled drive for wheeled vehicles, and self-cleaning wheels or drums on compactors to handle the material efficiently.
Factors Influencing Landfill Mobile Plant Selection
The choice of landfill mobile plant depends on several factors, including the type and quantity of waste, specific machinery requirements, the treatment status of the delivered material, and the availability of on-site materials for cover. Wheeled vehicles continue to be popular choices due to their versatility and effectiveness.
Certain features are essential when buying either vehicle;
(i) they should have cabs with roll-bars for the protection and comfort of the operator;
(ii) if a bulldozer is purchased, the blade should be designed for handling refuse it should be higher and wider, and should stand off from the vehicle further than is normal;
(iii) a cutting-wheeled vehicle (compactor) should be equipped with four-wheeled drive;
(iv) the fan should blow out from the engine instead of drawing air in, in order to reduce the risk of choking the radiator with refuse;
(v) the wheels or drums of a compactor should be self cleaning and suitable to deal with the material being imported.
The choice of the, general-purpose landfill mobile plant, depends on several factors; quantities and types of wastes;
- the activities required of the machinery;
- whether the material delivered to the site has been previously treated;
- location and nature of any materials on site which might be used for side or top cover.
Scrapers, both towed and independently powered, are seldom seen on landfills after initial development of the bases of landfills. They are used to strip, store and replace top and subsoil, and various forms of civil engineering earthworks equipment will clearly be used for such work including mechanical diggers and trenching equipment are used on site works.

Cost Considerations and Maintenance
Cost is a critical factor when purchasing landfill mobile plant. For tracked vehicles, track maintenance costs can be high due to the abrasive nature of the materials they operate on.
However, proactive vehicle replacement can help reduce costs and improve overall efficiency. Wheeled vehicles, while faster, may not match the high-precision levelling capabilities of tracked counterparts.
When selecting a vehicle for controlled tip work, operational expenses must be considered, as well as the level of work that the vehicle is capable of performing. Track maintenance costs for tracked vehicles can be high due to the abrasive nature of the material in which the tracks run, but costs can be reduced by changing the vehicle before major repairs are required and when the exchange rate is favourable.
The disadvantage of punctures has been overcome to some extent in wheeled vehicles, and is completely eliminated for steel-cutting wheel-equipped compactors; however, while they may be faster, they are not capable of the high levelling standards of the tracked vehicle.
Concluding on Landfill Compactors
Landfill compactors are essential pieces of equipment in waste management, aiding in the efficient and effective compaction of solid waste in landfills.
Landfill compactors have evolved significantly over the years, addressing early challenges and becoming essential in waste management. Understanding their history, features, and considerations for selection is vital for optimizing landfill operations.
By embracing technological advancements and making informed choices, waste management companies can enhance their landfill compactor performance and contribute to more efficient and sustainable waste disposal practices.
When considering the purchase and operation of a landfill compactor, it is crucial to factor in the initial purchase cost, ongoing maintenance and repair expenses, fuel and operating costs, and training and operator costs.
By understanding these essential features and costs associated with landfill compactors, waste management companies can make informed decisions and ensure the smooth operation of their landfill sites.
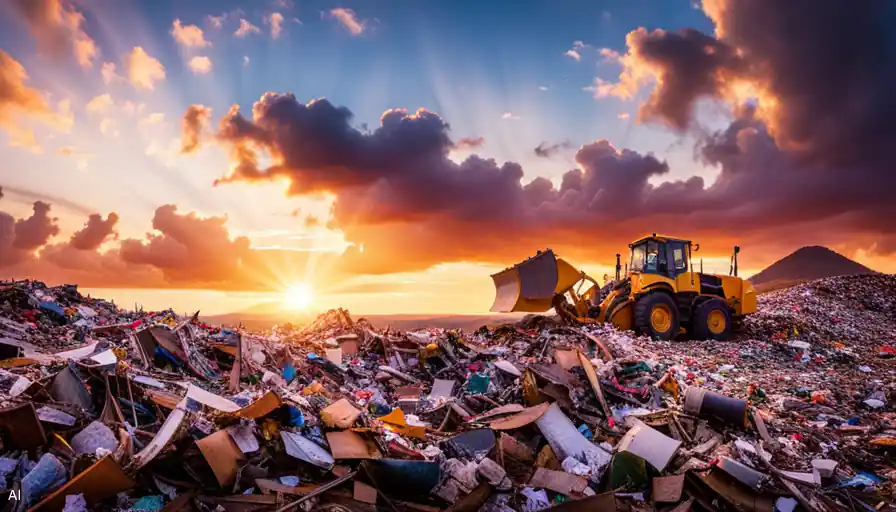
Landfill Compactors – Frequently Asked Questions
Q1. What is a landfill compactor, and what is its primary function?
A!: A landfill compactor is a heavy-duty machine designed primarily for efficiently compacting and reducing the volume of solid waste in landfills. It functions by using steel wheels equipped with spikes, lugs, or bars for compression and traction, allowing it to effectively compress waste material.
Q2. What are the essential features of landfill compactors?
A2: Landfill compactors typically possess the following essential features:
- Robust Construction: They are built with a heavy-duty frame and reinforced components to withstand the harsh landfill environment.
- High Compaction Force: These machines exert immense force on waste material to reduce its volume effectively.
- Spiked Wheels: Spiked wheels provide traction and stability, penetrating waste for maximum compaction force.
- Sealed Cab: Compactors have sealed, pressurized cabs to protect operators from hazardous gases and odors.
- Waste Management Systems: Many modern compactors feature advanced waste management systems, including onboard scales, GPS tracking, and telematics capabilities.
Q3. What are the main challenges faced by early landfill compactors?
A3: Early landfill compactors faced two primary challenges:
- wheels picking up refuse, especially in wet conditions, and
- instability due to their high centre of gravity.
Q4. How have modern landfill compactors overcome these challenges?
A4: Modern landfill compactors have addressed these challenges through design improvements, including carefully configured wheel spikes and advanced waste management systems. They offer reliable waste density when operated correctly and have enabled significantly increased efficiency in landfill operations by raising the density of the waste.
Higher-density waste in a landfill increases the capacity of the landfill and reduces subsequent settlement, improving the stability of the waste slopes.
Q5. What other equipment is commonly used in landfill operations?
A5: In landfill operations, you may encounter equipment such as scrapers, mechanical diggers, and trenching equipment for various tasks like soil handling and excavation.
Q6. What factors should be considered when choosing landfill mobile plant?
A6: The choice of landfill mobile plant depends on factors such as waste type, quantity, and site-specific machinery requirements, treatment status of delivered material, and the availability of on-site materials for cover. Key features include operator protection, specialized blades, four-wheeled drive, and self-cleaning wheels or drums.
Q7. What are the key cost considerations when purchasing and operating landfill compactors?
A7: Key cost considerations include the initial purchase cost, ongoing maintenance and repair expenses, fuel and operating costs, and training and operator costs.
Q8. How has technology evolved in landfill compactor design and performance?
A8: Technology has evolved in landfill compactor design, enhancing their efficiency and reliability. Features such as improved wheel spike configurations, and body designs to reduce turning circle diameters for improved manoeuvrability when filling small landfill cells, have contributed to better performance.
Q9. Is there any specific maintenance required for landfill compactors?
Proper maintenance is crucial for the efficient and reliable operation of landfill compactors. Regular servicing, component replacements, and repairs are necessary to ensure their longevity and performance.
Q10. What are the advantages and disadvantages of tracked vehicles compared to wheeled vehicles in landfill operations?
A10: Tracked vehicles are durable but may have high track maintenance costs due to abrasive materials. Wheeled vehicles are faster but may not match the high-precision levelling capabilities of tracked counterparts.
Q11. Conclusion: How can waste management companies optimize landfill compactor performance?
A11: Waste management companies can optimize landfill compactor performance by understanding essential features, embracing technological advancements, and making informed decisions regarding purchase and operation costs. This ensures efficient and sustainable waste compaction as part of the best waste disposal practices.
[This article was originally published on 23 June 2009, and was comprehensively rewritten and updated in January 2024.]
helloI really like your writing so a lot share we keep up a correspondence.
Back in the day, driving those early compactors, you’d find yourself battling with the wheels grabbing onto trash like there’s no tomorrow, especially when the ground’s wet. And talk about feeling like you’re about to tip over with that high center of gravity! We quickly learned that spreading the waste in thinner layers was the trick to dodging those headaches. It wasn’t just about the machinery adjustments; it was about how you approached the whole compaction game.