Table of Contents
ToggleDepackaging for Compost, or “Why Composting Companies Use a Depackager to Save on Labour Costs and Ensure High-Value Contaminant-Free Compost”
Composting has become an essential part of waste management, offering an environmentally friendly solution for diverting organic waste from landfills while producing nutrient-rich compost. However, as the variety of materials entering composting facilities increases—ranging from food waste to packaging and non-compostable items—managing contamination has become a growing challenge.
To address this issue efficiently, many composting operations have turned to depackagers.
These machines not only reduce labour costs but also ensure the production of high-quality, contaminant-free compost, benefiting both businesses and the environment.
Here's why depackagers have become a critical component of modern composting.
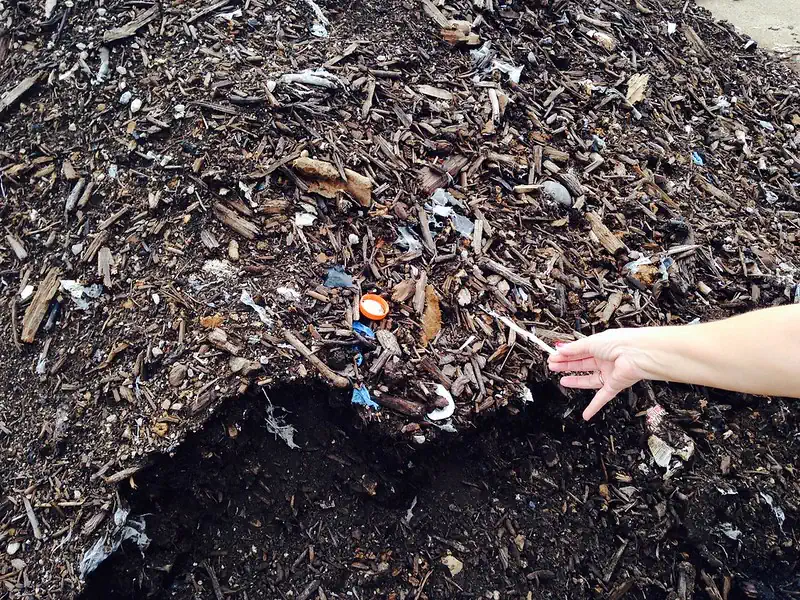
1. Reducing Labor-Intensive Contamination Management
In any large-scale composting operation, removing contaminants such as plastic packaging, glass, or non-compostable serviceware is a constant challenge.
Traditionally, workers had to sift through waste manually or rely on screening processes after composting. This can be labor-intensive, time-consuming, and not always effective in removing smaller plastic pieces that can degrade the quality of the final compost product.
Depackagers solve this issue by automating the front-end separation of organic waste from contaminants. These machines process materials like food waste in its packaging, breaking down the organic material while separating it from non-compostable items like plastics, metals, and glass.
This pre-processing step significantly reduces the amount of manual labour required to clean up the waste stream, as almost all of the contamination is dealt with before composting even begins.
By using a depackager to reject plastic items almost whole, including flexible plastic and films, and also heavy objects such as stone and large lumps of wood, composting companies can reallocate labour resources to more productive areas of the operation.
The reduction in labour costs is particularly beneficial for companies dealing with high volumes of food waste, where contamination levels are often high.
2. Improving Compost Quality by Minimizing Contaminants
The quality of compost is crucial for both environmental and commercial reasons. Contaminants like small plastic particles that are created by traditional compost chipping and screening machinery can reduce the value of the compost. It certainly makes it less appealing to end consumers, such as gardeners, landscapers, and agricultural operations.
Additionally, these contaminants now known a microplastic peices and nano-plastics pose severe environmental risks if they end up in the soil or waterways.
Depackagers ensure that the organic feedstock entering the composting process is free of contaminants, which improves the overall quality of the compost.
By batting or pulling out materials in an air-vortex like plastic wrap, non-compostable serviceware, and metal containers before they reach the compost pile, companies can produce a cleaner, higher-value product.
This not only increases customer satisfaction but also opens up opportunities for premium markets that demand contaminant-free compost for uses like organic farming and high-end landscaping.
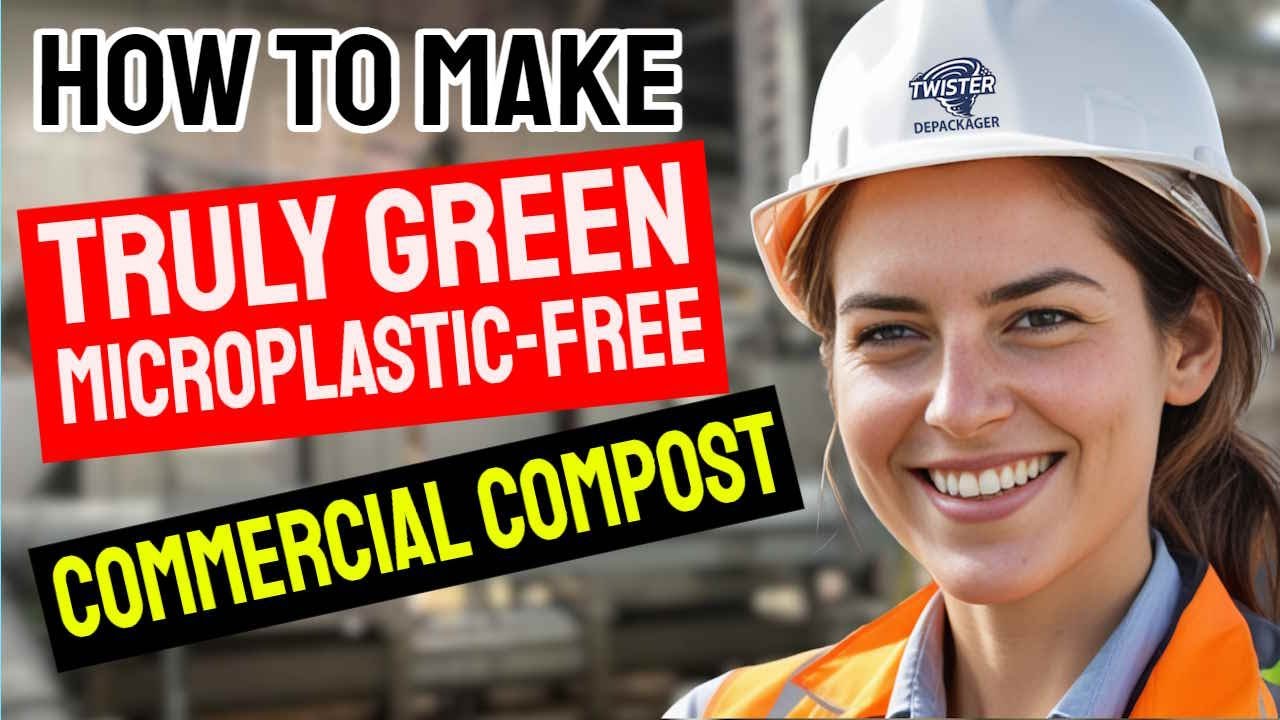
3. Enhanced Efficiency with Modern Depackaging Systems
Modern depackaging systems are designed to be both efficient and adaptable to different types of waste streams. These systems can process large volumes of mixed waste, handling various packaging materials and organic wastes simultaneously. Advanced machines can process anywhere from 7 to 15 tons of waste per hour, depending on the composition of the material.
For example, lighter materials like plastic bottles and metal cans are processed quickly, while heavier, wet food waste may take longer. However, with these systems in place, the overall efficiency of the composting process increases. By removing contaminants at the front end, the need for screening and manual sorting later in the process is minimized, further saving time and resources.
4. Boosting Environmental and Economic Benefits
Using a depackager also allows composting companies to align with zero-waste goals and maximize environmental benefits. By ensuring that rejected materials, such as plastics and metals, are diverted from landfills and sent for recycling or energy recovery, composting companies can reduce their waste footprint. Some facilities are even able to sell certain waste products as refuse-derived fuel, offering an additional revenue stream while contributing to energy recovery efforts.
Additionally, composting operations that invest in depackaging systems often gain a competitive advantage in the marketplace. By marketing their compost as contaminant-free and aligning with zero-waste initiatives, they can attract a broader customer base and potentially command higher prices for their premium products.
5. Future-Proofing Composting Operations
As the volume and complexity of organic waste continue to grow, especially with more municipalities and industries adopting composting as part of their waste management strategies, the demand for efficient contamination management will only increase.
Depackagers help composting facilities prepare for future challenges by offering a scalable solution to handle larger and more diverse waste streams for co-composting alongside green, yard, or garden waste.
The best of these systems are also highly customizable, meaning they can be adapted to the specific needs of different facilities. Whether dealing with food manufacturers, restaurants, or schools, depackagers must be able to manage a wide variety of waste types while ensuring that the composting process remains efficient and contamination-free.
Only the latest depackaging technology developed for this purpose is capable of doing this. One that is available on the global market is the Drycake Twister Depakaging system.