Understanding Mechanical MSW Processing the use of AI Sorting Technology, the increasing importance of organic waste, and the action necessary to enable a phasing-out of all existing shredding and milling technology is more important than ever before.
The world of waste management and recycling is evolving rapidly and with it, the technology used to process and recycle mixed municipal solid waste is changing. It also needs to change still further to avoid microplastic production.
In this article, we’ll be exploring the different mechanical processing equipment used in the recycling of mixed municipal waste and the importance of sorting techniques.
We’ll also discuss the need to phase out particle size reduction technology which uses shredding and screening to break down waste, as microplastics created by this method can be hugely damaging to marine ecologies.
The revolutionary manner in which AI is allowing multiple logic switches and greater flexibility in sorting, is also covered versus the common single-switch selectors built into purely mechanical sorting technologies.
Finally, we’ll look at some of the newer and more effective solutions, such as a third-generation organic waste and OFMSW (Organic Fraction of MS) depackaging system which can replace the old shredding and milling technology without creating microplastics.
Municipal MSW Solid Waste Screening
Screening is the process of separating materials into different sizes or types of materials. In terms of the Municipal Solid Waste mechanical processing equipment used to recycle mixed municipal waste, screening is the process of sorting through the waste stream and separating out the materials that can be recycled from those that cannot. Within an MRF (Materials Recovery Facility or Recycling Centre) the recyclable materials are then sent to the appropriate recycling line, usually by conveyor, for further processing.
Screening is a generic term and is accomplished in a variety of ways. At its simplest, it would be implemented by passing mixed waste over a steel mesh, or a metal plate with holes in it allowing the smaller items to drop through under gravity. In real life that would not work for long before the openings would become clogged, blocked up and ineffective. For that reason, an early development was the rotating drum screen.
Hand-picking at the start of a recycling line is a form of screening.
Rotating Drum Screens
Screening in drum screens has until recently been the core separation process for the processing of municipal solid waste. There are now alternatives such as vibrating tables, however, in this article, we will limit our discussion to drum screens which are also known as trommels.
A trommel is a screen that is curved into a cylinder. As material passes through, the machine rotates the screen to sort it. The material such as mixed MSW is in a tumbling motion throughout this operation. The MSW (paper, plastics, metals, grit, soil, organic matter, sand etc.) is separated as the smaller fraction falls through the holes. The cylinder is placed on a slight slope down to the discharge point, from which the larger fraction falls for further sorting.
Drum screens are mainly used for separation (known as pre-classification) of the incoming waste into a size range between 100 mm and 300 mm. Good selectivity can be achieved with separation sizes between 200 mm and 240 mm (Ref: 1).
In the coarse fraction material with a high calorific value is concentrated. This material has been used extensively for energy recovery in municipal incinerators and for sale as RDF. However, it is now common for extensive further sorting to take place in regional MRFs, as required in order for increasingly stringent recycling targets to be met.
If the current high use of plastic materials is to continue in a more sustainable manner, the ever-rising quantity of plastic items in the coarse fraction requires sophisticated separation into individual polymers (HDPE, PVC, PET etc.) as only then can the resin be cleaned and recycled. This is not easy to accomplish with the relatively clean and whole plastic items which tend to be seen in the coarse fraction after screening. It is even harder to separate source-segregated food waste if size reduction such as shredding or milling. In fact, it is not currently economically feasible after size reduction machinery. For this reason, alone, particle size reduction should not be applied. Instead, more modern technology now provides alternative methods to size reduction.
In the fine particle range separation takes place between 80 mm and 25 mm. The separating grain size is determined by the further utilization of the fine fraction. While the fine fraction should be relatively coarse for composting, it has to be <40 mm for dry fermentation processes (Ref: 1).
Protection against clogging and wrapping in drum screens
The use of drum screens for coarse screening causes big problems regarding the plugging of the screening media.
The open screening surface area (A0) can be reduced within a few hours to such an extent that considerable changes in mass flows are occurring. From different analyses, a plugging of up to 50% of the open screening area during one shift of eight hours is known. An appropriate measure against plugging is to use tube constructions which are welded from the outside onto the screen openings (Ref: 1).
This efficiency often amounts only to about 70 to 80 % in the plants although an efficiency of >95% could be realized. Accordingly, fine material is discharged via the overflow of the screen which has negative effects on the product quality.
The same effect is taking place if MSW, which is very difficult to screen due to a strong tendency to bind together, is screened at sizes <100 mm without a coarse pre-screening stage. Thus, considering the high importance of the screening step for the whole preparation process, a view on the size distribution of municipal waste by data collection and analysis for design purposes, subsequently is not only very useful but, we argue, necessary (Ref: 1).
Both, screen underflow and overflow products from mixed MSW show a completely different composition, the first enrich the organic components while highly calorific particles are mostly to be found in the coarse fraction.
Municipal MSW Solid Waste Shredding
What is Shredding?
Shredding is the process of breaking down large pieces of municipal solid waste into smaller pieces. It is done with mechanical processing equipment, such as a shredder, which uses a rotating blade to cut the material into smaller pieces.
The shredder has traditionally been used in the recycling process to break down materials like paper, plastics, cardboard, glass, and other recyclables into smaller pieces, so that they can be more efficiently sorted and recycled.
Shredding (and Milling) Makes Microplastics
It has now been confirmed by numerous scientific papers that the shredding and milling of Municipal Solid Waste (MSW) create microplastics that end up in global oceans. When these tiny pieces of plastic get into the water, they can cause major damage to freshwater and marine life.
Shredding also creates microplastics which are picked up and blown in the air. This can end up in our lungs and most human populations now contain a microplastic burden in their blood. Wind-blown microplastic also gets into the oceans.
Mechanical MSW processing is a major issue because it’s difficult, or impossible, to clean up microplastics once they’ve ended up in the ocean. Unless the formation of microplastics can be stopped during waste processing for reuse and recycling, the world will need to start using less plastic, and stopping shredding is one way that will help.
How the Global Recycling Industry is Damaging the Environment by Making Microplastics
There are many benefits to recycling, but it has become a problem because of the way plastic is recycled. The process of shredding MSW recycling begins by breaking down the plastic into small pieces so that it can be reused. Before the advent of Mechanical MSW Processing AI-based sorting techniques particle size reduction was essential, but that's no longer true.
However, when plastic is recycled into microplastics, the particles become so small that they are difficult to remove from the waste stream. These tiny bits of plastic are then released into the environment after Municipal MSW Solid Waste Shredding and end up polluting water sources and contaminating the food that we eat.
Microplastics have been found in every continent on Earth and are now being found in every ocean. They have even been found in the air, and studies have shown that they can be toxic to both humans and animals.
It is essential that we find a way to recycle plastic responsibly so that we can protect our environment and our health. Fortunately, there is new Mechanical MSW Processing Solid Waste Shredding depackaging and separation technology available from companies like Drycake™ Twister™ which has been developed to do just that and not create microplastics.
Municipal Solid Waste Sorting Technology
In mechanical processing plants for the treatment of municipal solid waste, the following sorting technologies are routinely used:
- Magnetic separation
- Eddy current separation
- Air classification
- Optical sorting technologies
- Organic waste depackaging and separation.
1 – Magnetic separation
Ferromagnetic substances in MSW like tin cans normally are separated very effectively using suspended magnetic belt separators. However, besides, tin-plate, a great variety of irregularly shaped components with large surface areas like plastic films are to be found in the feed mixture.
This causes strongly polluted “rejects” (scrap) products. Magnetic separators with alternating pole systems can provide much better separation results. Nevertheless, due to Mechanical MSW Processing cost reasons these technologies only are used rarely.
In order for the fine fraction of municipal solid waste to be treated biologically a high-efficiency separation of ferrous metals is necessary. Due to the difficult material conditions, a recovery of 95% is not possible in many cases. Furthermore, a lot of compound materials such as batteries are contained in the feed material which cannot be separated using conventional magnetic fields.
Here, the use of permanent magnetic neodymium drum separators is featuring good results. They are working with high field gradients and separate with high efficiency even small batteries, videotapes and ball pen cartridges.
Thus, the application of Municipal MSW Solid Waste magnetic separators has a veritably positive effect regarding the final content of heavy metals in the material to be treated biologically.
However, when separating a magnetic product by this measure the use and recycling of the ferrous product have to be clarified. As the strong field is also attracting weakly magnetic items, the product is contaminated with small non-magnetic particles and wet organic ingredients.
Therefore, a further sorting step is usually necessary, in order to clean the magnetic product.
2 – Eddy current separation
In recent years intensive development took place in the field of non-ferrous metal separation by eddy currents.
Today, eddy current separators preferably should be applied with eccentrically arranged pole wheels in the head pulley and modern high-intensity permanent magnets based on neodymium-iron-boron (Ref: 1).
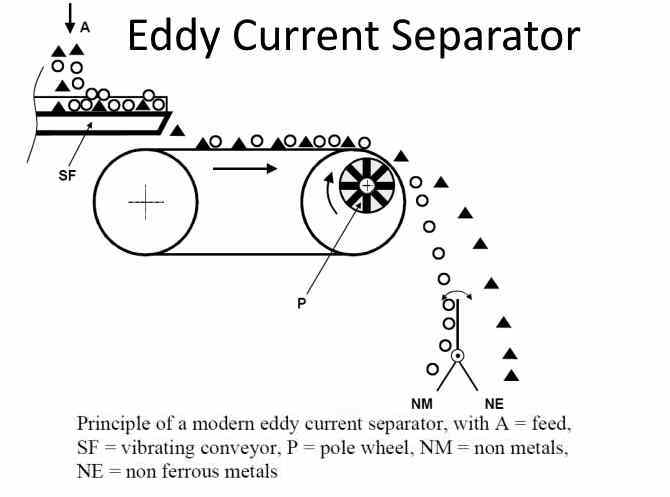
Due to the number of pole pairs and the high frequency of the alternating magnetic field (up to 1000 cps) the sorting of non-ferrous metals from waste material mixtures with grain sizes as small as 1 mm is possible (Ref: 1).
The items fed onto an eddy current separator have to be isolated from each other as the separation requires a single grain layer on the belt in order to avoid cross-contamination.
Therefore, for isolating the particles it is very important that a preceding screen, sizing and feeding with a vibrating conveyor, is taking place.
The most important kind of non-ferrous metal contained in MSW is aluminium which can be found in the form of cans, different packaging items, or for example, bottle caps.
The Mechanical MSW Processing Al-yield can be as high as 90%, and the grade of the NF-product depends strongly on the waste mixture and the pre-treatment.
A content of 60% – 70% aluminium-based particles can be achieved, as especially aluminium often is used in combination with other materials e.g. in beverage cartons or toothpaste tubes, therefore the aluminium content of the product typically is low (Ref: 1).
Thus, further treatment of this product by e.g. pyrolysis is required.
3 – Air classification
As a simple technology for the efficient sorting of airborne constituents from waste mixtures air classification is used.
Here, the fact is taken into account that a certain amount of household waste components with a high calorific value such as paper or plastics mainly occur in the form of foils. This shape criterion is much more important for this sorting process than the density.
Besides shape and density, the structure of the different material groups is important for the Mechanical MSW Processing system's air classification, too. (E.g. textiles are especially absorptive for humidity within the collection containers thus showing a high density compared to plastic foils.)
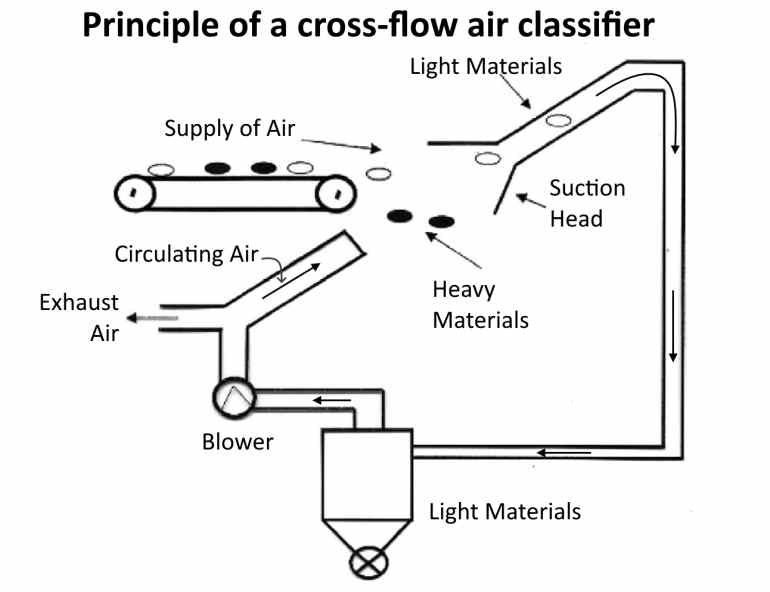
While zig-zag air classifiers commonly were used at the beginning of MSW processing. Today the cross-flow air classifier which can be seen in the figure is the most important sorting installation (Ref: 1).
Cross-flow air classifiers are operated with partly re-circulating air. The amount of fresh air comes up by 30%. With construction as a blower and sucker, a very high-quality fuel (high combustion calorific fraction) can be concentrated which contains mainly plastic foils, thin body-type plastics and dry paper.
The yield of light material is at least 70%. The limiting factor is the density of the load which generally should not exceed 350 g/m³ of air per hour. From typical household waste material, 10-15% of RDF with high calorific value can be concentrated (Ref: 1).
If the air classifiers are used for bigger particle sizes (>240 mm) high potentials are existing for disturbances within the pneumatic transport of the light fraction. Furthermore, plugging due to very large single particles cannot be avoided as the profile of the air separation chamber is limited (Ref: 1).
In this case, simple blower constructions have proved to be useful where the blower ejects the air into the material flow from above. This “elongates” the flight trajectory of the light material components while heavier or body-shaped particles are not influenced (Ref: 1).
4 – Optical AI-based sorting technologies
For more than 20 years optical sorting with automated picking is known for the Mechanical MSW Processing of cullet into different colours.
As a detection system, the measurement of transmission has been used there. During the last few years, many developers have been looking for new detection techniques.
Especially the advantages of image detection and near-infrared (NIR) detection have to be mentioned here. These techniques can be realized only now as powerful computers are available which can handle large amounts of data very rapidly.
The NIR-sorting systems can be used for the selective separation of components with high calorific value like plastics, paper, cardboard, nappies (diapers), wood, and beverage cartons.
The isolated waste particles are transported via a belt conveyor below a light source with a velocity of up to 2.5 m/s. A detector identifies the NIR spectrum of the particles (Ref: 1).
If for example a desired type of plastic is identified, the process computer gives a signal to an air nozzle system which is located at the end of the transport belt. With a short air blast, in ballistic separation, the particle is blown out of the flight trajectory and discharged separately to Mechanical MSW Processing (Ref: 1).
The detection system and the air nozzles are subdividing the belt cross section into elements with a width of about 10 mm thus providing the sorting of particles within a wide size range. The frequency of detection is higher than 10.000 per second. The time for single nozzles to be toggled is about 10 ms. With this, a powerful technology is existing which allows throughputs of 8 to 10 tons per hour with a machine width of 2.000 mm (Ref: 1).
Figure 3 shows the principle of an automated picking system with NIR detection.
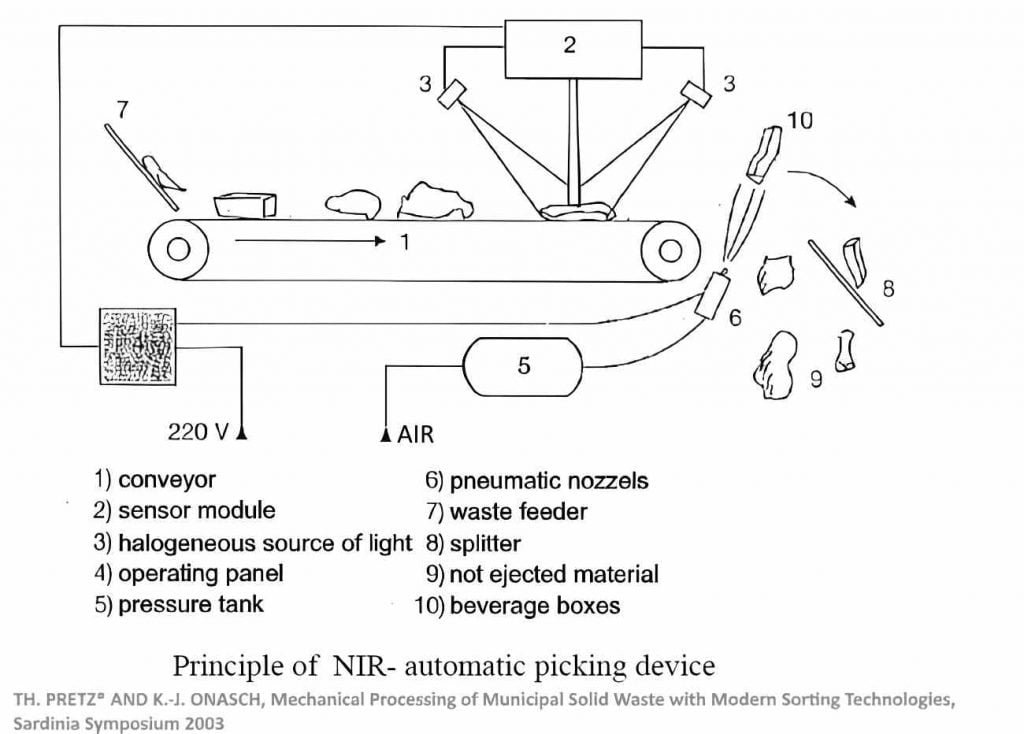
Principle of the NIR- automatic picking device
The use of optical sorting for the processing of packaging waste material during the past few years has led to very good experiences with these new technologies. Today, the spectra of many types of plastics including different disturbances caused by pollutants such as dirt or water are programmed.
The optical sorting machines also allow the separation of single types of plastics selectively. This makes e.g., the negative sorting of PVC possible thus influencing the parameter of chlorine concentration which is a main parameter specified for RDF compliance for use in boilers. Besides the sorting of plastics with a yield of over 80% it is also possible to detect cellulose such as wood, paper, cotton or cellulose from diapers with NIR (Ref: 1).
Due to stronger Mechanical MSW Processing disturbances, the yield is much lower at 50 to 60%, though (Ref: 1).
Sometimes detecting single particles only by NIR is not sufficient. Recently developments allowed a combination of NIR detection with picture analyses using highly sophisticated cameras.
Sorting machinery with these features is able to separate particles with very special characteristics, e.g., differing from the type of used colour or even selecting on viewing a printed surface design.
Comparing the traditional separating technologies using different material conditions like shape or density with the “new” technology of automated picking, there must be remarked one main difference.
Automated picking technology allows separating according to the specific quality of each product that can be found in waste mixtures. These self-learning AI systems can evaluate typical parameters for different detecting tasks. However, the “old” mechanical technologies can only separate according to one main and some additional or overlapping attributes. Therefore, both the efficiency of separating processes like air separating or vibration separator and the quality of sorting products which was limited, but that’s no longer true when AI systems are used.
If a technology is used that separates according to the attributes hard or flexible, a flexible PVC particle will be discharged in the “light” product, while a hard PVC tube will enter the “heavy” product. The result of the preparation process is a limited selectivity for PVC.
So, the introduction of automated picking processes in the rough field of operating municipal waste has brought a new level of quality to waste processing.
5 – OrganIc Waste Depackaging and Separation
Organic waste depackaging and separation is the process of sorting and separating organic waste from non-organic materials. This process typically involves removing the packaging, such as plastic or cardboard and then separating the organic waste from the non-organic waste.
Organic waste is then sorted according to type and further processed for composting, anaerobic digestion, or other use. Depackaging and separation equipment helps to reduce the amount of landfill waste and the resulting methane emissions. It also makes organic waste easier to manage, recycle, and compost.
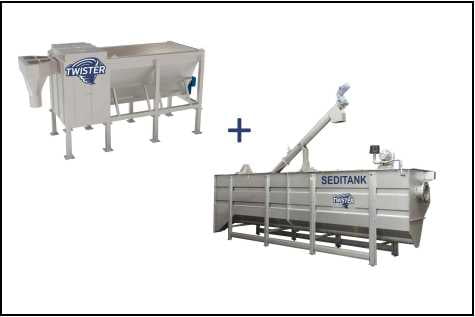
No other machine can perform the mechanical sorting that shredding previously offered as well as the TWISTER™ De-packager and Separator.
Without reducing particle size, it separates packaging from food or other organic substances, such as OFMSW.
Instead of being shredded in conventional systems, plastic objects, flexible plastics, and films are separated from the pulp and appear in a reject stream, torn and damaged but generally whole, or in discrete pieces. Thus, the Twister prevents the production of more microplastic. The contents are taken out of pots, packs, and even bags.
It operates by use of a vertical rotator, only the bottom part of which is immersed beneath the incoming trash. All large and heavy items are propelled out of the mixed trash at the speed of rotation using a ramp or wedge at the bottom of the rotator, where the activity begins.
The Mechanical MSW Processing rejects are propelled upward and out of the device by precisely angled vanes that are mounted to the rotator and continue the upward motion.
With clinging food, moisture, and filth being violently pushed off by the powerful swirling movement and bouncing on the ribbed outer wall of the machine, plastic emerges wonderfully clean.
A proprietary technology prevents flexible plastic and films from winding around the rotor, producing a reject output that may be sent to a typical MRF recycling machine. There, it is easily processed using the customary methods of air grading, optical sorting, magnetic and eddy current separation, and when needed, magnetic and eddy current separation for the highest recycling yield.
By choosing plastic bottles with the highest income potential from high-end polymers like PET, HDPE, etc.
Water addition is not required for Twister Mechanical MSW Processing. A strainer mesh surrounds the device as the pulp output exits it.
Any water addition is optimised for the amount of water preferred for anaerobic digestion, and a Drycake™ Seditank™ Unit may be added if the microplastic content of the incoming waste exceeds end-use specifications for the digestate (after energy extraction in the biogas plant).
Mechanical MSW Processing – CONCLUSIONS
The processing of household waste material (MSW) can be realized with high efficiency today.
Well-established sorting technology such as modern magnetic and eddy-current separators and optical sorting systems can be used to recycle a number of materials for the production of high-quality recycled products.
Besides metals especially the production of a fraction with high calorific value (RDF) is interesting and much improved plastic resin recycling is possible.
By using modern processing technology like the Drycake Twister technology for the production of such RDF fractions a high yield and good qualities can be achieved without jeopardising the environment with microplastics.
References:
- Proceedings Sardinia 2003, Ninth International Waste Management and Landfill Symposium, S. Margherita di Pula, Cagliari, Italy; 6 – 10 October 2003. Pub: 2003 by CISA, Environmental Sanitary Engineering Centre, Italy