How to use compost depackaging systems to produce microplastic-free commercial compost.
Everyone hates finding bits of plastic in commercially available garden compost. The good news is that efficient depackaging and separation machinery is now available to remove plastic bags and miscellaneous plastic items. So, for the sake of the environment, the composting industry should cease all pre-shredding of organic content before composting.
Hand-picking to remove plastic from the compost reception area is labour-intensive and tedious work that has never been sufficient for plastic removal. Now that depackaging and separation machinery has improved, the composting industry no longer needs shredding machines to conceal the plastic.
A new generation of the latest non-shredding, non-milling, and non-cutting depackaging machines is here to remove these impurities first so that they never enter the composting process.
This blog will show you how these systems are used to remove plastics from commercial compost, making it cleaner for our earth.
It's time for compost plant operators to cease their seldom-discussed practice of small particle shredding. Shredding will, of course, always be needed to reduce particle size for use in horticulture, including for potting plants, and seedlings. But repeat shredding simply to hide the visibility of plastics by cutting them into very small pieces that won't be noticed, should be a thing of the past.
Keep reading to learn more!
Key Takeaways About Compost Depackaging
- Producing compost at commercial windrow and in-vessel composting sites without first using a depackaging machine is an outdated practice.
- Low-impact depackaging systems are available that don't create microplastics are available to efficiently remove, not only plastics but all manner of other unwanted non-organic materials.
- The Twister depackager and separator is one example. It has a rated throughput capacity of 5 to 15 tons/hour but usually handles about 7 tons/hour at most typical commercial composting site locations.
- Rejected material from the depackaging process gets sold as refuse-derived fuel (RDF) to, for example, co-firing cement kilns, turning waste into energy. Increasingly, the clean rejects from the depackager/separator are sold for plastic resin recycling into new products.
- Missouri Organic Recycling (MOR) uses a compost depackager to remove plastics from compost. They started using it in 2018.
- MOR extended their composting process duration to enhance quality. Total active composting now takes them about 6 weeks, with an additional curing time of up to 3 months.
[boomdevs_toc]
The Problem of Microplastic in Commercially Produced Compost
Compost produced commercially from source-separated organic waste, such as garden waste, parks park department waste, and food waste, previously revered for its role in improving soil health and fertility, is now a major source of environmental concern due to microplastic contamination.
Microplastics, or plastic particles smaller than 5 millimetres in size, routinely find their way into compost mixes, mostly through persistent ignorance or a lack of care by the general population for the well-being of the environment.
This happens when gardening and when scraping food waste from their plates. This includes all types of packaging materials that are found in the collected organic waste stream. Typically many more unwanted waste material classifications will also be present, albeit usually in small quantities.
The result is that not only does commercially produced home garbage contribute to microplastic contamination, but so do agricultural practices that use peat-free compost mulches for land-spreading as a sustainable fertiliser and soil improver.
While the latter two benefits of compost cannot be denied, in the long term, the issue of microplastic contamination is very serious and needs to be urgently addressed.
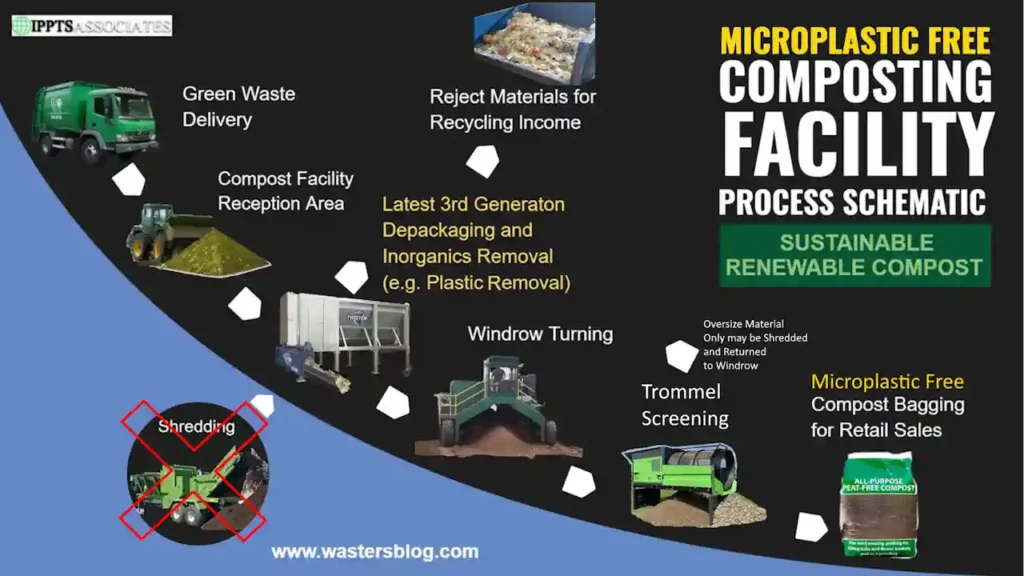
The risks from microplastics in compost identified by recent scientific research
The utilization of municipal solid waste (MSW) compost in agriculture is, in principle accepted to be, an environmentally sound method for repurposing organic waste.
However, there is a growing body of scientific evidence (ref. 1) that the presence of physical contaminants, particularly plastics, poses significant risks.
These contaminants, including glass, metal, and stones, can originate from various sources and accumulate in compost due to inadequate separation and sieving processes.
Plastics are of particular concern, as they are prevalent and can contribute up to 536 kg/ha/year of plastics to soils, leading to severe environmental and soil health risks.
The “Plastics and other extraneous matter in municipal solid waste compost”, study (ref. 1) highlights the urgency of addressing these contaminants through:
- improved waste management practices to ensure pre-treatment of green and other organic waste to remove plastics before composting commences,
- regulatory compliance, and
- the adoption of only those compostable materials that have been pre-treated to safeguard soil health and environmental quality.
Now let's see how they added compost depackaging into their operation at MOR.
Incorporating Depackaging into a Composting Operation
Integrating depackaging pre-treatment to remove all unwanted/non-organic items before the commencement of the composting process by investing in a 3rd generation depackager is the way it will be done in the future.
Rejecting the contaminants before anything else makes it possible to produce a virtually plastic-and-metal contamination-free, premium retail-quality compost.
The rejected material is sold as refuse-derived fuel or will command a good price as in-demand recyclable plastic.
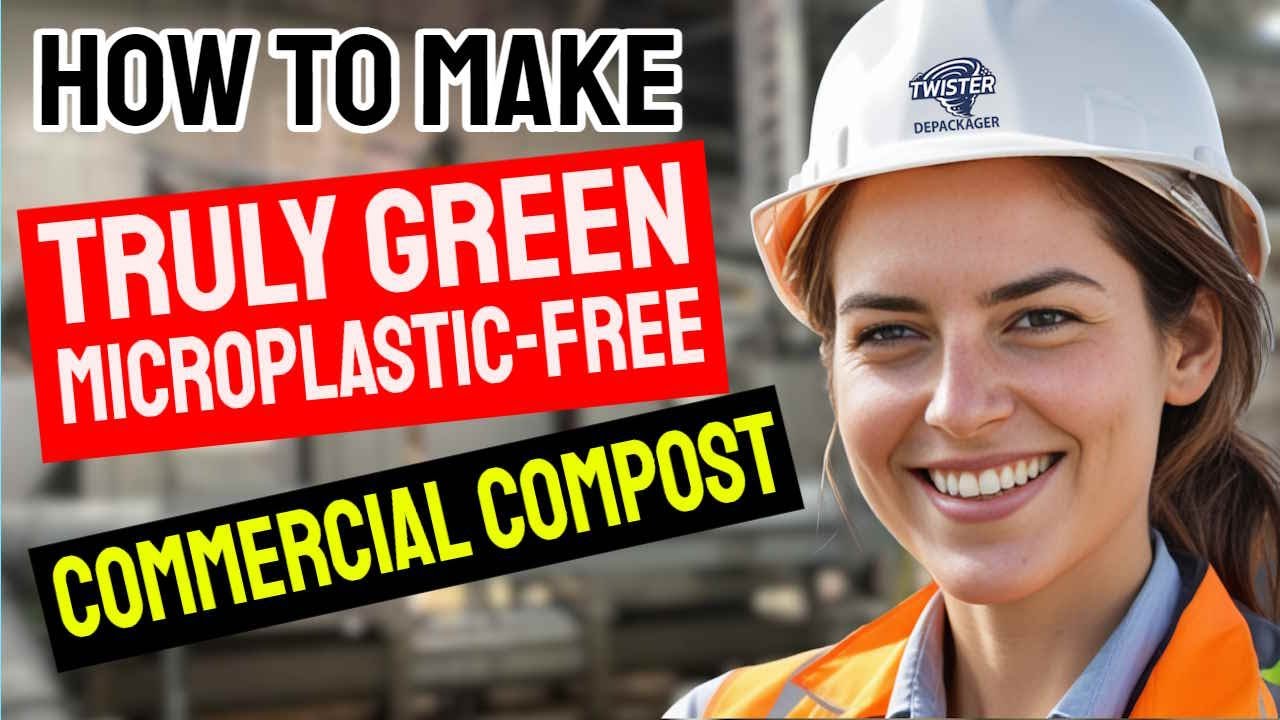
Case Study: Premium quality compost output leads to expansion of operations
The market for peat-free compost is huge and growing rapidly. That's because of rising public awareness of the severe climate change impacts from the over-use of peat-bog peat which has been reducing the global carbon stored in those bogs.
Missouri Organic Recycling has made big steps in growing its work. They brought a new depackaging machine, that was set into into action in 2018. This tool has helped them sort out 14% of the content in source-separated food scraps that couldn't be used for composting, right from the start.
It has meant that not only is their compost product free from concerns about adding to plastic in the environment, it means they can now take more types of waste to turn into compost. Their goal to manage pollution better and accept more materials is working.
They also got help with money from a grant worth $50,000 in 2005. They used this to buy a big tanker lorry for collecting liquid waste from places that make food. MOR handles about 17,000 tonnes of unwanted food and around 85,000 tonnes of plant debris each year now.
This shows how much they've grown since the beginning of the business in 1992. Now within their bigger operations, they make an impressive 75,000 cubic yards of compost every year.
Next up, is how MOR added an initial depackaging step to make their compost products even better.

Compost Depackaging Case study pilot project
The Missouri Department of Natural Resources funded a special trial before the compost depackaging machine project began. This test involved working closely with a local salad-packing business starting in 2001. It was set to run for two years.
The goal was to see if they could handle leftover food and packaging waste better.
This project opened doors as long ago as 2004, allowing more types of kitchen scraps and unwanted packaging to be accepted. They wanted to make less trash ending up at the dumpsite and use it instead to create nutrient-rich soil additives.
This pioneering effort was successfully aimed at making composting methods more effective while keeping tiny bits of plastic out of our gardens and fields.
Rejection of contaminated material
After MOR brought the depackager into their composting operation, they were able to tackle the problem of contaminated material head-on. The depackaging machine identified 14% of the food waste as unsuitable for compost due to contamination.
This unwanted matter comprises non-biodegradable items that can't be broken down in a compost system.
MOR found a clever use for these rejected bits. They found that they could mix them with dried broken wood from pallets. Then, they sell this blend to a nearby cement kiln as refuse-derived fuel.
This approach not only keeps the contamination away from their compost but also provides an alternative energy source for another industry, turning waste into something valuable again.
Sale of rejected material as refuse-derived fuel
MOR sells the unwanted material from the depackaging process to a nearby cement kiln. This material becomes refuse-derived fuel. It's a smart way to handle waste that can't be composted.
Selling it helps avoid landfilling and reduces methane emissions.
The move turns problems into power for industrial uses. Next, we look at the equipment helping MOR turn organic waste into valuable compost.
Efficient Depackaging Equipment for Composting Plant Uses
Family-run depackaging and separation equipment company Drycake supplies state-of-the-art Twister depackaging equipment for microplastic-free composting facility operation.
This advanced machinery streamlines the process and ensures high-quality compost production. For more details, keep reading.

Typical Equipment frequently used for composting facility operation
Commercial composting facilities process large volumes of mostly local authority-collected garden waste. They typically use a variety of machines to make compost. These devices are essential to ensure that the compost reaches the required high temperatures required to kill the seeds and pasteurize the compost for reasons of hygiene. Turning the compost regularly is most important to ensure a homogeneous product of consistently high quality, making it a useful soil additive.
The most frequently used machinery at any industrial composting facility includes:
- Front End Loaders: These vary in design from general farm duty tractors to purpose-built bucket loading machines. These loaders are used to move large amounts of materials around the site and to fill the hoppers of depackaging machines, and shredders. They are essential for handling large quantities of organic waste and the resulting compost.
- Skid Steers: These compact loaders are versatile and used for a range of tasks, such as loading smaller amounts of material or cleaning areas where bigger machines can't go. Both Front-end Loaders and Skid Steers can be used for turning the compost although they're not as efficient as a dedicated compost turner design for this task.
- Compost Turner: This special machine stirs and aerates piles of composting material, speeding up the decomposition process by ensuring each part gets enough air.
- Hogzilla Tub Grinders: These grinders break down large pieces of organic waste into smaller bits that decompose more easily. They're powerful and can handle a wide range of materials.
- Peterson Horizontal Grinders: Similar to tub grinders, these machines also reduce the size of compost materials, but in a horizontal position, making them suitable for different types of waste.
- Power Screen Screens: After grinding, these screens help separate finished compost from larger pieces that need more time to break down. This ensures only the finest material gets through.
- Doppstadt Trommel Screens: Another type of screening equipment, these rotate to sift through materials, separating out usable compost from larger items that aren't fully decomposed yet.
- Large Vertical Tanks: MOR installed three tanks with a total capacity of 29,000 gallons for storing liquids used in the composting process or captured rainwater for moisture control.
- Potable Water Tank: At MOR they installed a 40,000-gallon tank that holds clean water crucial for adjusting moisture levels in the compost piles, ensuring they stay at optimal conditions for decomposition.
- Meyers Custom-Built Mixer: This device at MOR mixes different types of organic wastes together before they go into the composting process, ensuring a consistent and quality mixture for decomposition.
These tools together create an efficient system that turns food waste and other organic materials into valuable compost while keeping operations smooth and productive at commercially operated green waste composting facilities.

Windrow turning process
After handling the equipment for composting, let's delve into the windrow-turning process. This process involves the windrow turner making at least three passes to form the windrows. Turning ensures that the whole pile is exposed to enough air to heat up and decompose throughout the whole of the compost batch into a consistent compost quality.
It should be noted that after facing initial challenges with this procedure, MOR invested in additional tanks and mixers to ensure smoother operations.
Case Study: Missouri Organic Recycling (MOR) in Kansas City, Missouri
The MOR composting operation in Kansas City, Missouri, was able to expand its operations and received approval for a pilot project, leading to securing a grant from MODNR to prove the viability of depackaging machines at the start of the operation. before windrowing commences.

Longer static pile period
As a result of the funded studies, MOR lengthened the static pile period and extended the total composting process duration. This alteration was done to enhance compost quality by allowing for more thorough decomposition.
By holding the material in static piles for a longer time. The entire active composting process took 6 weeks, and then there was up to 3 months of curing.
In the UK, PAS 100 provides the standards for the composting process, input material selection, minimum composted material quality, and compost product storage, labelling, and traceability. It provides the requirements for a QMS (Quality Management System) to generate composts that are consistently suitable for their intended usage.
Total composting process duration
The total active composting process takes about 6 weeks. This duration allows for thorough decomposition and transformation of organic waste into high-quality compost suitable for various applications.
Following this stage, the curing of compost can range from 3 weeks to 3 months, enhancing its quality and nutrient content.
At all these sites, getting the right balance of airflow, moisture levels, and temperature during this time is important for encouraging the good microbes that are needed for decomposition to happen quickly and make a nutrient-rich and fertilising product.
Capacity and throughput of a typical compost depackaging unit
Capacity and throughput of the depackager matter a lot in managing green waste and food waste alike. The 3rd generation non-microplastic generating Twister depackager and separator is a key device in the process.
The experience at MOR shows us how effective this approach can be:
Feature | Details |
---|---|
Rated throughput capacity | 15 tons/hour |
Average throughput capacity | About 7 tons/hour |
Online since | 2020 |
Immediate impact | Removed 14% of the food waste stream as contamination |
Limitations | Still learning; Best for splitting containers not larger than 1-gallon |
They have found that the depackager’s role can be crucial for the success of a new composting facility.
Right away, once the depackager was commissioned, it sorted out 14% of waste as “rejects” not suitable for breaking down biologically. Their machine can process up to 15 tons every hour. But on average, it handles about 7 tons. Its best use is with small containers, ideally no bigger than 1 gallon capacity.
Understanding how this machine helps when handling garden prunings and food waste was a revelation to the farm business.
Compost Depackaging Conclusion
In summary, the experience of Missouri Organic Recycling (MOR) encourages everyone to embrace the use of depackagers to enhance their composting operation. The company's strategic rejection of contaminated material before composting starts by using depackaging equipment was found to be a wise one.
The current successful sales of the fibrous portion of the digestate as refuse-derived fuel have demonstrated their commitment to sustainability, while also producing microplastic-free commercial compost.
With an extended static pile period and a longer total composting process, at the time of commission, MOR stated that they intended to continue to unlock the potential of compost depackaging systems for a cleaner, more sustainable environment.
This innovative approach underscores MOR's dedication to waste management and landfill diversion while heralding a new era in compost production.
References:
Ref. 1 – Okori, F., Lederer, J., Komakech, A. J., Schwarzböck, T., & Fellner, J. (2024). Plastics and other extraneous matter in municipal solid waste compost: A systematic review of sources, occurrence, implications, and fate in amended soils. Environmental Advances, 100494. https://doi.org/10.1016/j.envadv.2024.100494
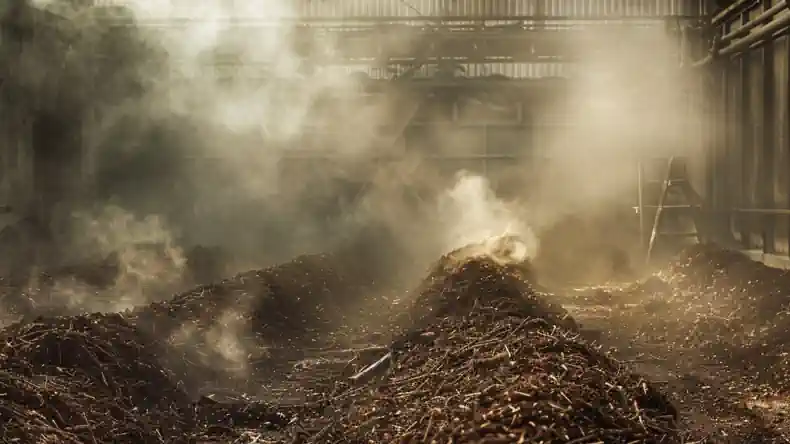
Compost Depackaging FAQs
1. What is a compost depackager?
A compost depackager is a machine that removes packaging from food waste and other organics before they are processed into compost, helping to reduce microplastics in the final product.
2. How does compost pretreatment help with waste management?
Compost pretreatment, including depackaging, helps by breaking down waste more efficiently for anaerobic digestion or biogas production, reducing the need for landfilling.
3. Can compost depackaging prevent plastics from entering commercial compost?
Yes, by removing packaging materials early on, especially non-compostable plastics and films, we can make commercial compost free of microplastics and safer for use in soils.
4. Why is it important to divert organic waste from landfills?
Diverting organic waste from landfills reduces greenhouse gas emissions and prevents valuable resources like food wastes from being wasted. It also limits the amount of microplastics that enter our environment.
5. Do anaerobic digesters play a role in creating microplastic-free compost?
Anaerobic digesters break down biodegradable material without oxygen, turning organics into digestate that can be used as nutrient-rich fertiliser or soil conditioner while capturing biogas for energy.
6. How do wastewater treatment facilities benefit from source-separated organics (SSO)?
Wastewater treatment facilities can process SSO more effectively than mixed municipal solid waste because it's easier to manage and treat organically separated materials without contaminants like plastics or metals.